
Internetowy sterownik kotła - bruli.pl
Cechy sterownika bruli.pl
zdalna obsługa i ustawianie parametrów pracy regulatora kotła z każdego miejsca na świece przy pomocy przeglądarki internetowej
kontrola i ograniczanie temperatury spalin w oparciu o logikę rozmytą (fuzzy logic)
aktualizacja oprogramowania sterownika przez internet
ustawianie parametrów serwisowych pracy regulatora oraz kalibracja czujników przy użyciu przeglądarki internetowej
rejestracja na karcie pamięci alarmów i innych zdarzeń
rejestracja na karcie pamięci parametrów pracy kotła
ustawianie temperatury normalnej (dziennej) i obniżonej (nocnej) dla centralnego ogrzewania i ciepłej wody użytkowej w cyklu dobowym i tygodniowym
regulator pogodowy z możliwością ustawienia temperatury normalnej (dziennej) i obniżonej (nocnej) w cyklu dobowym i tygodniowym
regulator pokojowy z możliwością ustawienia temperatury normalnej (dziennej) i obniżonej (nocnej) w cyklu dobowym i tygodniowym
możliwość współpracy z termostatem pokojowym
niezależne zabezpieczenie termiczne kotła przed niekontrolowanym wzrostem temperatury
Więcej informacji na stronie bruli.pl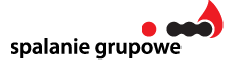
Spalanie grupowe w kotłach centralnego ogrzewania z palnikiem automatycznym zasilanym paliwem stałym
Spalanie paliw stałych w kotle z palnikiem automatycznym jest procesem bardzo trudnym, zarówno ze względu na niejednorodność paliwa pod względem fizycznym np. wielkość cząstek - uziarnienie, jak i zmienność parametrów fizykochemicznych istotnych dla procesów spalania.
Szczególnie trudnym paliwem jest paliwo węglowe, którego właściwości zależą nie tylko od źródła pochodzenia – kopalni, ale nawet od pokładu z którego jest wydobywane. Proces spalania paliwa węglowego w automatycznych kotłach jest procesem stochastycznym.
W znanych rozwiązaniach w kotłach automatycznych na paliwo stałe dawkowanie paliwa, a przez to i spalanie traktowane jest jako proces ciągły. Oznacza to, że podajnik pracuje w regularnych i powtarzalnych cyklach pracy i postoju, a zmiana mocy odbywa się wyłącznie przez zmianę proporcji czasu pracy i czasu postoju podajnika, co w żadnym wypadku nie wpływa na regularność powtórzeń.
Wadą podejścia do procesu dawkowania paliwa jako procesu ciągłego – a przez to i spalania – są potężne problemy z dobieraniem proporcji paliwa i powietrza ze względu na procesy stochastyczne procesu spalania oraz to, że podawane są kolejne porcje paliwa w tak niewielkiej odległości czasowej od siebie, że nie można ocenić czy poprzednia dawka uległa dopaleniu. Znaczące wydłużanie czasu między podawaniami zawsze musi się wiązać, dla uzyskania odpowiedniej mocy kotła, ze znaczącym wydłużeniem czasu podawania dawki co powoduje chwilową stratę niezupełnego spalania widoczną w postaci dymu.
W wyniku badań procesów spalania w kotle automatycznym na paliwo stałe nieoczekiwanie stwierdzono, że podejście do procesu dawkowania paliwa – a przez to i spalania – jako procesu impulsowego (dyskretnego) pozwala dokonać oceny, czy poprzednia dawka uległa dopaleniu.
Zmiana traktowania procesu dawkowania paliwa – a przez to i spalania – nie jako procesu ciągłego tylko impulsowego jest zmianą rewolucyjną.
Realizacja nowego sposobu sterowania polega na grupowym powtarzaniu cykli podawania i krótkiego postoju podajnika, po których następuje długa przerwa pozwalająca na dopalenie dostarczonego wcześniej paliwa, a moment dopalenia określany zostaje na podstawie analizy trendów temperatury spalin.
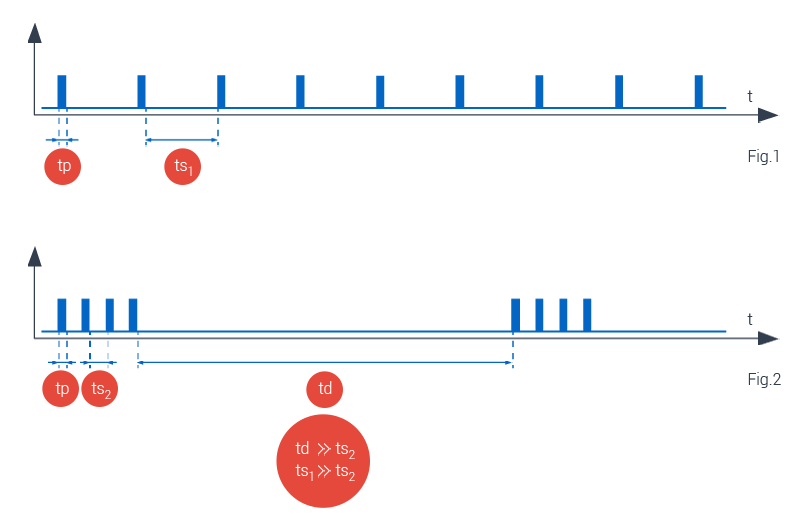
Fig.1 – klasyczny sposób podawania paliwa
Fig.2 – grupowe podawanie paliwa
Dla ułatwienia obsługi zostało zdefiniowanych 5 mocy (8 kW, 12 kW, 16 kW, 20 kW i 25kW) z jakimi może pracować kocioł. Każdą z mocy charakteryzuje odpowiednia ilość podawanego paliwa cyklu. Użytkownik musi jedynie dobrać obroty dmuchawy dla wybranych przez siebie mocy.
Algorytm regulatora przełącza kocioł pomiędzy dwoma zdefiniowanymi mocami (między minimalną i maksymalną mocą) w zależności od zapotrzebowania na ciepło. Wybór dwóch (pary) mocy należy do użytkownika. Jeśli kocioł ma pracować z jedną mocą należy ustawić moc min i max na tą samą moc. Parametry podtrzymania pozostają standardowe.
Zaletą nowego podejścia jest optymalizacja procesu spalania paliw stałych dla różnych typów kotłów, różnych podajników i dmuchaw.
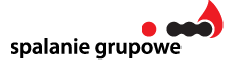
Jak czytać histogram dla spalania grupowego
Histogram to jeden z graficznych sposobów przedstawiania rozkładu empirycznego cechy. Składa się z szeregu prostokątów umieszczonych na osi współrzędnych. Prostokąty te są z jednej strony wyznaczone przez przedziały klasowe (patrz: Szereg rozdzielczy) wartości cechy, natomiast ich wysokość jest określona przez liczebności.
W naszym przypadku na osi X zgrupowane są czasy postoju podajnika o rozdzielczości 10 sek. Im wyższy słupek, tym więcej razy wystąpił określony czas postoju. Z lewej strony histogramu mamy krótsze czasy postoju zaś z prawej strony czasy dłuższe.
Czasy postoju są zależne od intensywności pracy dmuchawy – im wyższe obroty dmuchawy - tym proces spalania jest szybszy, im niższe obroty dmuchawy – tym proces spalania jest wolniejszy.
Czas postoju nie może być za krótki – zbyt intensywne spalanie (lewa strona histogramu) oraz zbyt długi – zbyt wolne spalanie (prawa strona histogramu).Rozłożenie słupków na histogramie dokumentuje działanie algorytmu spalania grupowego. Jeśli wysokie słupki pojawią się przyklejone do prawej strony histogramu świadczy to o tym, że algorytm nie wykrywa w założonym czasie dopalenia paliwa - świadczy to o zbyt małym nadmuchu.
Podane informacje mają pomóc w ustawieniu mocy dmuchawy w procesie spalania grupowego.
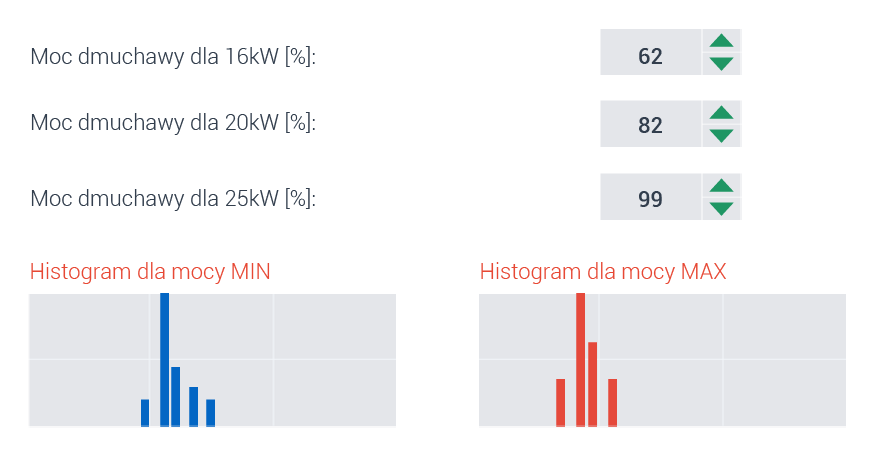
Pliki do pobrania dla bruli.pl
Lp. | Nazwa | Format |
1. | Instrukcja obsługi - bruli.pl | |
2. | Gwarancja - bruli.pl | |
3. | Operating manual - bruli.pl | |
4. | Návod k obsluze - bruli.pl | |
5. | Bedienungsanleitung - bruli.pl | |
6. | инструкция по эксплуатации - bruli.pl | |
7. | bruli.pl Updater 0.1.17.22 | EXE |
8. | bruli.pl strona WWW 0.1.9.20 | ZIP |